您所在的位置:首页›划重点 | 罗姆第四代碳化硅技术的进化及其三大优势
划重点 | 罗姆第四代碳化硅技术的进化及其三大优势
日期:2023-02-20
2月14日罗姆举办“2023年媒体线上交流会”,罗姆半导体(上海)有限公司市场宣传课高级经理张嘉煜和技术中心副总经理周劲分别介绍了罗姆公司最新动态和碳化硅(SiC)功率器件的演进,以及第四代碳化硅技术和产品。
投资增至四倍,旨在扩大产能
前不久,罗姆董事长松本功表示:“由于脱碳化和资源价格高涨,汽车的电动化需求增强,碳化硅产品的需求提前了两年。”话音未落,2022年年底,罗姆就在日本福冈县正式量产碳化硅功率半导体,以此开拓纯电动汽车及医疗等新兴市场。
据报道,罗姆计划到2025财年(截至2026年3月)向碳化硅功率半导体投资2200亿日元,投资额增加到2021年计划的4倍。松本功认为,通过建设新工厂等增产投资,该公司的份额将提高到30%。目前罗姆碳化硅功率半导体的全球份额为14%左右。根据Omdia数据,罗姆功率半导体全球份额排在第10位,碳化硅产品排在第4位。
过去几年,罗姆碳化硅举措不断,从2020年开始,先后与纬湃科技合作开发碳化硅电源解决方案;与臻驱科技(上海)建立联合实验室;碳化硅器件被吉利逆变器选用并签署战略合作协议;与正海集团签署协议成立碳化硅功率模块合资公司;被UAES认证为逆变器碳化硅功率器件解决方案首选供应商;SiC MOSFET被应用于Lucid Air的OBC;第四代SiC MOSFET通过赛米控eMPack®模块认证……这么多的合作当然需要有先进技术和足够的产品支撑。
张嘉煜透露,具体到碳化硅市场,罗姆2025年度的销售额目标将超过1100亿日元。预计从2024-2026三个年度有近9000亿日元的市场有待开拓。为了实现这样的目标,罗姆正在不断进行碳化硅方面的投资,除了将美洲作为主要市场,欧洲和中国也是主要目标市场。
碳化硅器件市场地位由来已久
罗姆是当之无愧的碳化硅器件技术领导者,在罗姆看来,碳化硅功率元器件是一种改变世界的技术。早在2000年,罗姆就创造了多项世界先进的技术,改变了世界碳化硅功率元器件格局;2004年开发出SiC MOSFET原型;2007年罗姆、京都大学、东京电子宣布开发出碳化硅外延量产技术;2010年推出世界先进的SiC SBD并率先量产SiC MOSFET;2012年量产世界先进的全SiC功率模块;2015年量产世界先进的沟槽结构SiC MOSFET;2017年量产6英寸SBD、推出车规级平面型SiC MOSFET;2018年推出世界先进车规级沟槽型SiC MOSFET;2020开发第四代沟槽结构MOSFFT。这些先进技术均已融入量产产品并已投放市场。
.png)
事实上,不少海外大厂往往将原料生产和半导体及外围零部件的开发分割开来。罗姆则遵循自己一贯的做法,于2009年收购了碳化硅晶圆产量第二位的供应商SiCrystal,完成垂直整合生产体系,以保证SiC产品的稳定供应及产品质量。多年来,罗姆在开发和生产两个方面坚持投资的做法已结出了硕果,包括碳化硅材料到完成品碳化硅模块都实现自行开发和生产。
如张嘉煜所说,罗姆的“一条龙”生产体制保证其从硅锭的采集到晶圆生产、IP内核设计、光掩膜制造、引线框架制作到最后产品的各种封装都是在自己工厂里完成,就连半导体生产设备都是自主研发。
.png)
在技术方面,罗姆不断提升碳化硅元器件的性能,并以晶圆、芯片、分立产品和模块等丰富的供应形式投放市场,不仅如此,还配以能够更大程度发挥元器件性能的栅极驱动器等外围电路解决方案,引领行业实现更具创新性的节能和小型化应用。
第三代到第四代SiC MOSFET的演进
近年来,新一代电动汽车的进一步普及促进了更高效、更小型、更轻量电动系统的开发,特别是对在驱动中发挥核心作用的主逆变器,进一步改进功率器件成为重要课题之一。2010年罗姆推出首款平面型SiC MOSFET,2015年第三代SiC MOSFET产品中率先量产双沟槽结构,积累了更丰富的基础研究经验,并迅速建立了从晶圆到元器件设计和封装的管理开发生产体系。
与IGBT模块相比,第三代产品的开关损耗降低了77%,与第二代平面MOSFET模块相比,开关损耗可以降低42%。第三代SiC MOSFET兼具极其优异的低损耗特性与高速开关特性,功率转换效率更高,有助于实现设备的节能化、小型化和轻量化。
第四代SiC MOSFET是罗姆于2020年完成开发的,在改善短路耐受时间的同时实现了业内超低导通电阻,不仅可供应裸芯片,还可供应分立封装产品。该产品有助于实现车载逆变器和开关电源等各种应用的小型化和低功耗。其特点有三:
一是改善短路耐受时间,同时实现业内超低导通电阻:通过进一步改进罗姆自有的双沟槽结构,成功地在改善短路耐受时间的前提下,使导通电阻比以往产品降低约40%。实现了业界SiC MOSFET超低的导通电阻。
二是通过大幅降低寄生电容实现更低开关损耗:通过大幅降低芯片内的寄生电容,成功地使开关损耗比以往产品降低约50%。
.png)
三是支持15V栅源驱动电压,使应用产品的设计更容易:在MOSFET中,需要在器件导通时向晶体管的栅极施加一定量的电压。除了第三代SiC MOSFET所支持的18V栅源驱动电压(Vgs)外,第四代SiC MOSFET还支持更容易处理的15V栅源驱动电压,可与IGBT一起用来设计驱动电路(栅极驱动电路),有助于设备进一步节能。
第四代产品彰显三大优势
周劲详细介绍了罗姆第四代SiC MOSFET的三大产品优势。
一个优势是低损耗。他介绍说,从第二代到第三代特征导通电阻(RonA)降了50%,从第三代到第四代,目前又降了40%。导通阻抗不断降低,使开关特性得以改善,实现了低损耗。在同等芯片面积下,第三代的导通阻抗大约是30毫欧,第四代为18毫欧,使损耗降低了40%。
.png)
第四代SiC MOSFET在同等导通阻抗下降低了栅极和源极间电容值(Cgd),实现了高驱动频率(高速开关)的优势,进而使发热量减少。通过降低开关损耗,还能够实现高驱动频率,使外围器件及散热器小型化。容量比(Crss/Ciss)的改善有助于抑制MOSFET器件的误开通和自关断,能够保证芯片更高速的开启和关断。
.png)
在应用中,如果将第三代SiC MOSFET替换为第四代产品,在重视导通损耗的场合,推荐选用同等高温下额定电流的产品。例如用30毫欧换成18毫欧导通阻抗可降低40%导通损耗;在重视开关损耗的场合,推荐使用25℃额定电流的产品,以便改善开关特性,明显降低开关损耗。
这是因为,在一种场合,应考虑同等器件高温时的额定电流,罗姆产品凭借RonA优势可以获得低导通电阻,实现全负载范围的高效率。而在第二种场合,在高频率开关条件(Fsw 100kHz)下,罗姆产品的开关损耗小,也可以实现全负载范围的高效率。
.png)
第二个优势是使用简便。开启(Tun ON)推荐栅极驱动电压(正电压)为8V-15V,使与IGBT等共用栅极驱动电路成为可能。之所以能够实现低电压驱动,是因为第三代产品为15V和18V驱动的导通阻抗差是30%,也就是说如果用IGBT通用的15V电压驱动不能实现SiC MOSFET的理想状态。第四代的15V与18V两种驱动电压的导通阻抗差只有11%,在15V的情况下就可以基本满足碳化硅全负载驱动。而在导通损耗非主要因素的轻负载条件下,栅极电压15V或18V的转换效率差较小;在重负载状态下,18V仍有优势。
.png)
对于负偏压设计,罗姆产品的栅极阈值电压较竞品高,在高温时(结温175℃)时也能避免自开启的风险,无需负偏压,使用也更安心。降低由寄生电容耦合至栅极的能量导致的栅极电压抬升,也能够有效避免自开启。无需负偏压设计的好处在于简化了栅极驱动器电路,降低了成本;变压器设计也得以简化,多输出栅极驱动器电源设计更加简便。
.png)
在同一外部栅极电阻值状态下,第四代SiC MOSFET开关损耗(Eon,Eoff)比同类产品小,降低了内部栅极阻值,使外部栅极电阻的调整更为灵活,电路设计也更加灵活,更容易满足客户需求。在相同栅极电阻阻值状态下,开关损耗也比同类产品小很多。
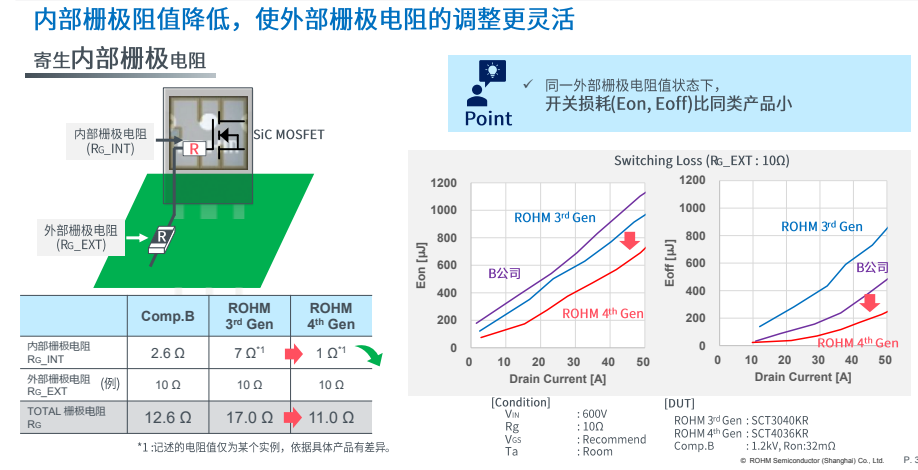
与第三代650V耐压同类产品相比,第四代产品750V耐压(Vds)设定使得耐压裕量更高,可简化浪涌吸收电路,减少器件数量,降低吸收电路带来的能量损耗,降低成本的同时,提升系统效率。
第三个优势是高可靠性。上面说过,第四代SiC MOSFET采用独特的器件结构突破了RonA与短路耐受时间(SCWT)的折中限制,实现了比同类产品更高的短路耐受时间。降低RonA后,通常饱和电流会上升,短路时的峰值电流也会上升,短路耐量时间变短;罗姆第四代产品在降低RonA的同时使饱和电流下降,短路时的峰值电流较低,成功延长了短路耐受时间。
.png)
正是因为有了上述优势,罗姆第四代SiC MOSFET具有低开关损耗、低恢复电流且低噪声以及低导通损耗的特点。这些高速开关SiC MOSFET非常适用于有小型、轻量化需求的车载充电器应用;较小导通损耗的SiC MOSFET非常适用于采用LLC电路的电源应用。
未来发展值得期待
罗姆先进碳化硅半导体器件路线图的近期目标是增加晶圆直径,提高生产效率,同时增加元件尺寸,支持高输出逆变器。2025年计划量产导通电阻降低30%的产品,并利用绿色创新基金加速第六代产品的研发,到2028年计划量产导通电阻再降低30%的产品。
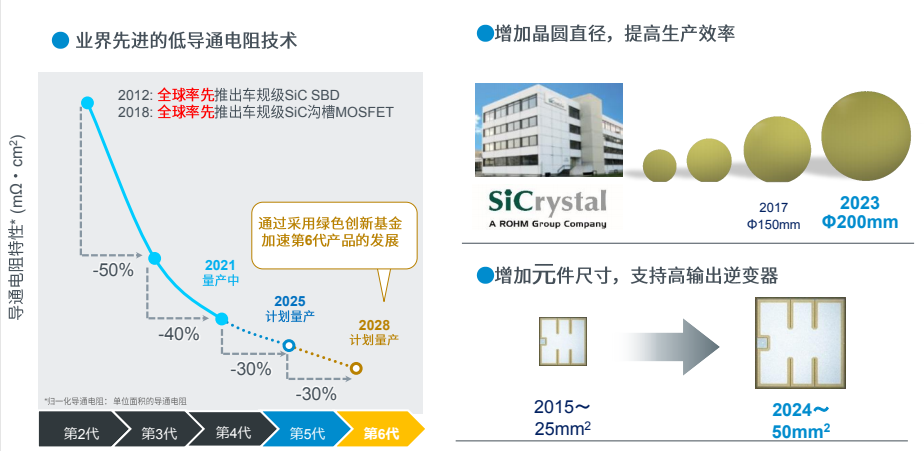
至于碳化硅器件和模块开发路线图,罗姆将在两年内将进一步丰富各种产品,2025年推出第五代沟槽型1200V产品,2026年推出第五代沟槽型750V产品。
作为碳化硅领域的先行者和领航企业,罗姆致力于改变世界的碳化硅功率元器件研发,不断追求更高的目标,以创新来满足越来越多的功率应用场景需求,为社会发展和实现“双碳”目标贡献力量。
推荐行业新闻更多